Continuous Improvement
Burns Bridge has enjoyed a career working as an agent of change and a process or continuous improvement leader. Burns Bridge can help you with your process improvement needs and offers the following insights to this process.
With the spread of Japanese manufacturing (now known as lean manufacturing and most recently lean six sigma) techniques across the world the continuous improvement process has become a structural part of most modern businesses. However, the innovation and improvement process has always been integral to human technological progress over the past two millennia. How else could humankind have progressed from the stone age to its current state?
With free trade starting to spread around the world starting more or less in the 1990's, for example, with the negotiation of NAFTA, a significant amount of
moral hazard was removed from the workplace. With free trade comes intense competition on a world scale. Managers quickly realized that improvement and innovation were critical to survival.
Further even though inflation has dropped below 2% per annum world wide, employees everywhere still expect some sort of small annual wage increase. Since it is not possible generally to pass on such increases in competitive markets, sales growth together with vital improvements in quality and productivity, are the financial means to meet these inflationary salary expectations.
Continuous improvement involves change and in every organization employees resist change vis a vis the graphic below for example.
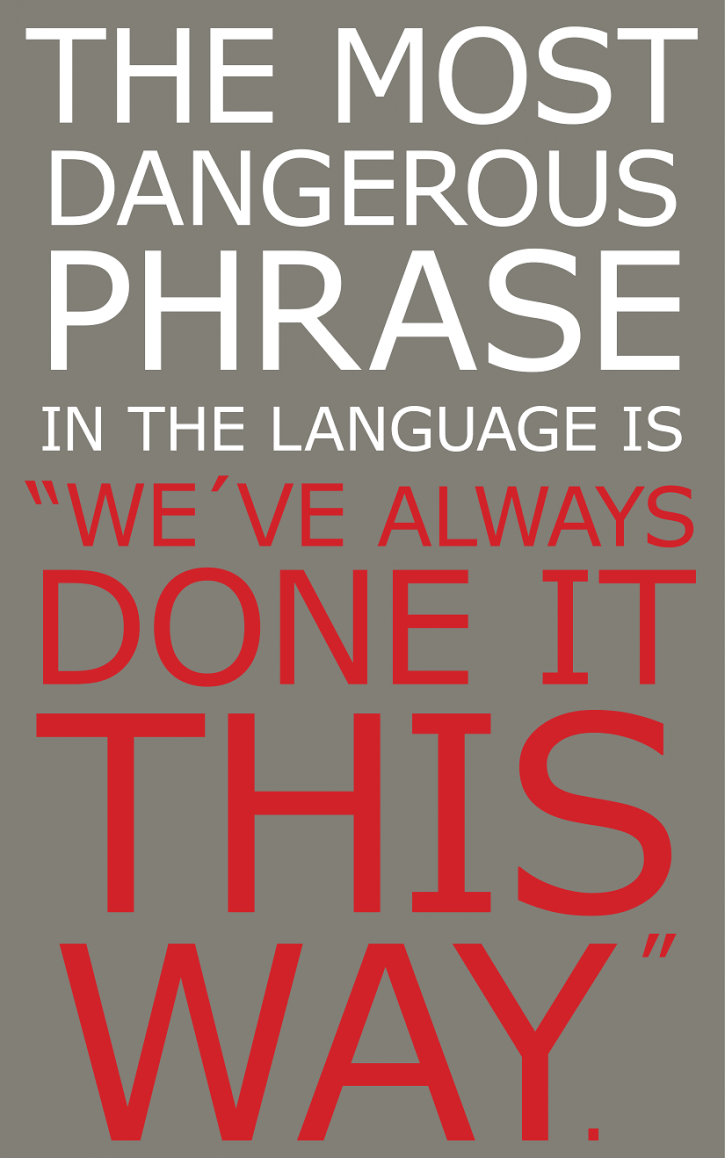
The majority of employees find change to be stressful and prefer to have a static work environment where nothing changes. Many employees love mind numbing repetition, in contrast to many motivational theories which suggest that workers must have a stimulating work experience. If an organization is under competitive pressure and must reduce costs by trimming the work force, employees will indulge in numerous dysfunctional behaviours to protect their jobs. In contrast, if job security is not at risk, workers will participate whole-heartedly in the improvement process.
Employees can be divided into four groups when it comes to their work variation preferences as follows:
- Those who like no change at all. These employees enjoy highly repetitive tasks such as pick and place or assembly jobs.
- Those who like some change. These employees enjoy repetition but are more comfortable tending to a group of machines where there is no pick and place and where on a periodic basis they have to service the process, by changing tools, making adjustments etc.
- Those who like change. These employees tend to be skilled trades who for example are involved in troubleshooting and maintaining a wide array of equipment.
- Those who dislike any repetition. These employees tend to be technologists and engineers who work on a wide variety of problems and assist skilled trakes when requested.
The principal of Burns Bridge has worked as an "agent of change" for over 38 years and is experienced in implementing change and continuous improvement programs in a wide variety of environments. Typically there are three approaches that can be used.
One person acting alone.
A cross-functional group created to solve a problem or complete a change project.
A Kaizen Blitz.
1. Single person change project: 1. A 3.1/3.4 litre V6 cam finish machining line in a south central Ontario automotive OEM engine plant had a lobe grinding bottleneck. The line had nine lobe grinders serviced by one operator per shift. The line had been in operation for several years. One of the lobe grinders had not run in almost as long a time. The maintenance group had given up on fixing the problem. As a result of the down grinder, the line was working structural overtime on weekends to remain on time. The cams were being shipped to Mexico for use in an engine assembly plant. Problem solving (statistical engineering) training was being taught to select shop floor employees, engineering staff and supervisors. Having completed the training, the general tool setter, the next day tackled the down grinder problem using "component swap" solution strategy. On his own he commandeered electronics technicians to remove an electronic controller from an obsolete grinder and reinstall it in the problem grinder. Within hours the grinder was running. No supervision or management involvement was present.
The use of a committee in this instance given the team culture which seeks to satisfy the wishes of each team member would have had a high probability of failure after months of non-productive committee meetings. In this instance one employee acting alone was able to drive a solution to a several year old problem in a couple of days.
2. As a second example a high volume automotive tier 1 fuel and brake line bundle fabrication plant had a first time through leak test failure problem on one of two leak testers on the line. The good leak tester had a 100% first time through metric while the problem unit was executing a retest 50% of the time. This loss was causing a significant loss of productivity. Numerous attempts were made to solve the problem. In the end, committee discussions were dropped and a reward was offered to the maintenance mechanic of two cases of his favourite beer on Friday. On Monday morning the problem had been fixed. On the weekend the mechanic performed a component swap of the electric servo spool pneumatic valve blocks between the two leak testers. With this swap the problem moved to the good machine indicating that there was something wrong with that valve block. On disassembly an o-ring sealing component was missing allowing air to leak out of the assembly. Productivity on the line improved by 15-20% immediately. A quality spill risk (type II error) was eliminated. The reward in this case was trivial considering the financial benefit to the plant productivity. However it presented the mechanic with a challenge to fix something where everyone else had failed and reap a fun reward.
2. Cross-functional group project: An OEM high energy pump repair centre in Western Canada had a quote preparation lead time of over 55 days in a business where customers considered 20 days to be acceptable. A group of staff were assembled to deal with this common cause structural problem consisting of the site manager, repair coordinators (quote preparers), shop leadership and the manager of the internal coating operation. The following key reasons were quickly established as causing the delays:
Lack of training for the repair coordinators; they knew almost nothing about the subject matter of their work.
Lack of a robust process for stripping tungsten carbide coating.
Lack of a document system for dimensional and visual inspection of the pumps and appropriate forms for reporting exceptions needing redress.

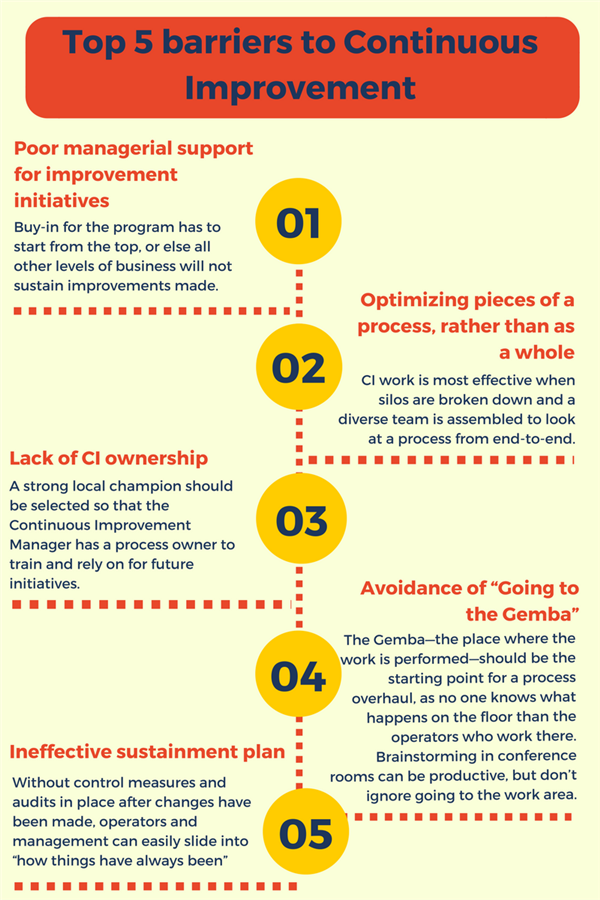
The above graphic summarizes key reasons why a CI program can fail to produce results. As a rule a strong leader having good problem solving skills is needed. Training of group members on basic problem solving skills is also essential. However in a group of 10 students in a problem solving class it is probable that only one or two will pick up the baton and run with it. One to two change agents in a group of 10 are more than enough provided a strong leader is present to keep the process on track.
Finally some sort of document is needed to track the process. Many companies use a simple RAIL (reaction action item log sheet) to track the continuous improvement process. Ideally a peer review meeting is conducted once a month where individuals report progress on each project. Some project items may be solved in days, weeks or months, while other more challenging problems could take 1.5 to 2 years before a path forward is divined. Projects may morph into something completely different depending upon the latest information. An example of a very simple partially completed RAIL is shown below.
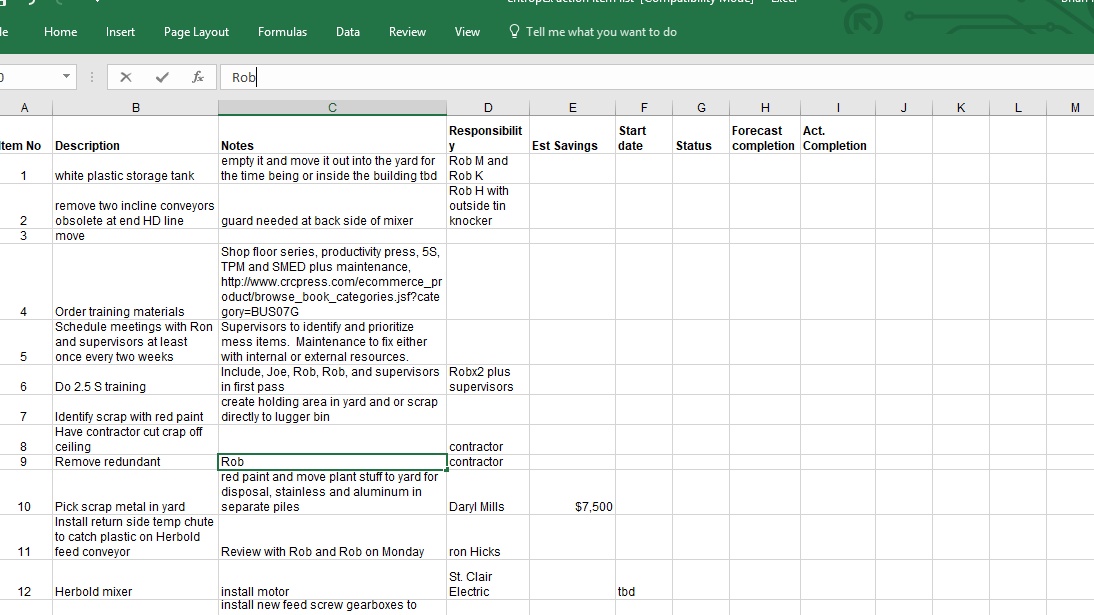
Closing Comments: Employee participation in a continuous improvement program is only possible if there is no risk of job loss. If there is risk of job loss, all employees will refuse to participate and if forced to do so, will try and sabotage obfuscate and obstruct the process.
Even if there are no job security issues, employee participation will vary greatly from employee to employee. For example in any group of 20 employees typically only two are motivated to improve things. These are the change agents whether or not they have received any change training or problem solving training. The rest of the employees are typically the silent majority who will go along for the ride. These individuals are typically happy with the status quo and are comfortable repeating a routine each day.
A continuous improvement program requires work and effort to keep on track. Many may find the meetings to be an irritating interruption to their routine.
There are three priorities in any business as follows:
Existing business (work in process)
New business (work in the quoting queue)
Continuous Improvement.