Problem Solving Methodologies
Comments: Continuous improvement is a critical part of every organization today whether it be a manufacturing, processing or services type business. However in order to improve things a manager must divine what needs to be improved. Often a list containing many items is prepared. In winnowing this list to the important few, a bottleneck analysis combined with a Pareto analysis must be conducted.
Bottle neck analysis, or The Goal, a book by Eli Goldratt is discussed in detail on "The Goal" page of this web site. Briefly, the Goal is to Make Money. More money is being made if, inventory decreases, throughput increases or total cost decreases. Unless a bottleneck is being mitigated, there will be no benefit to the company. Such non-bottleneck items must be winnowed from the continuous improvement list.
Pareto Analysis suggests that 20% of the problems cause 80% of the variation. Often the 20% is actually one root cause explaining 80% or more of the variation. To achieve the greatest benefit to an organization all bottleneck projects should be ranked from top to bottom with the items having the most financial impact at the top of the list. The one exception to this is any unsafe behaviour or unsafe condition. Safety items must be addressed immediately where appropriate.
Once a list of problems or opportunities have been assembled there are a number of problem solving strategies available to establish a root cause and eliminate the problem as follows:
Six Sigma
Kepner Trego
Shainin
Statistical Engineering, University of Waterloo
The New Science of Fixing Things
Six Sigma: This problem solving strategy also known as "Zero Defects" was popularized originally by Motorola and then later by General Electric. Initially it was branded as a business process re-engineering tool where it was used to eliminate indirect and direct non-valued added costs by by process re-engineering. More recently the acronym DMAIC has become it's core problem solving strategy.
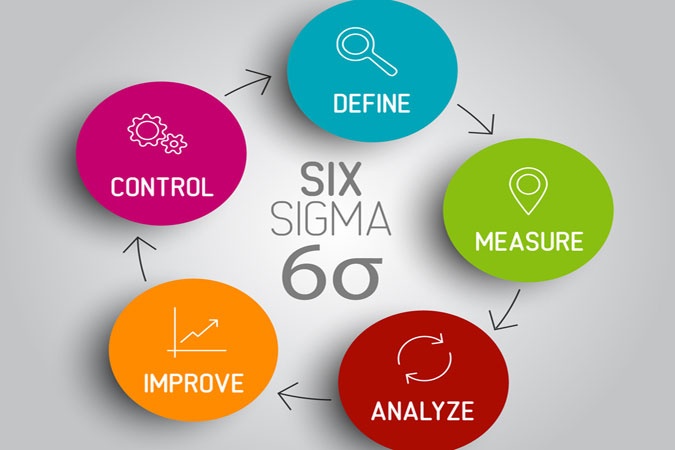
Six Sigma System Comments: While this methodology has its place in solving certain types of problems, there are a number of concerns which a senior executive should consider before assigning organizational resources:
- Training is time consuming and expensive. Students typically receive a month or more of long distance training provided by specialized consultants which charge large fees.
- The methodology requires a college or university level understanding of statistics in order to perform complex statistical analysis and write the time consuming and detailed reports.
- Yellow, green and black belt projects take months to complete and document, usually six months or more.
- The program relies on black belt specialists to complete most projects with a black belt specialist needing to complete each of one or more yellow, green and then black problem solving projects to obtain certification.
- The black belt title confers the image of that of a "guru", to whom other employees in the organization delegate or defer all problem solving and improvement change activities.
- The black belt specialists tend to regard themselves as special, spend a lot of time in phone calls and meetings talking about their program and accomplishing very little.
- Many months delay are involved before any measurable financial results are accrued.
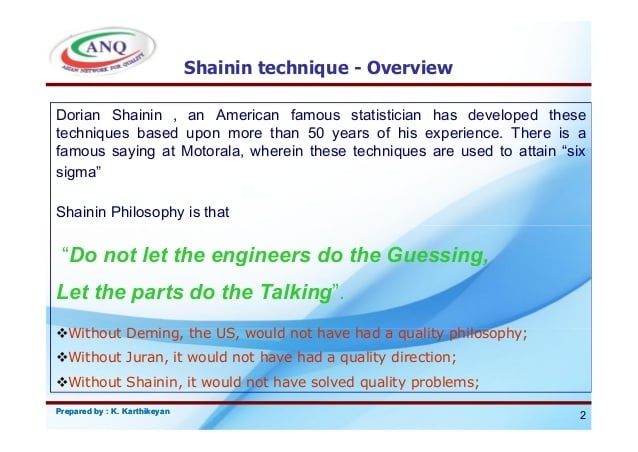
Burns Bridge regards the Shainin method as a very powerful and cost effective problem solving methodology. Best used in volume manufacturing, its techniques can also be used carefully in an engineered to order environment. The methodology starts with a well defined very specific problem definition statement and then uses a multivariate decision tree having families of variation as vertical columns to drill down into the tree eliminating all families except one using a tool box of perhaps 50 tools to collect and analyze data to identity the red "X" or dominant root cause. The importance of the problem definition statement cannot be over-emphasized. Incredibly, in many organizations, which are not performing well, the general manager, often, does not know what is wrong.
The techniques used are simple, graphical and easy to use. Most importantly a low level understanding of math and statistics is needed. There is not much in the way of report writing and training is typically one week or less (three days normally). Students having grade 8 or 12 math can apply the techniques on the floor to solve problems. Most problems can be solved in 30 days or less. Typically a few days are all that is needed to identify a root cause and solve a problem. The techniques are very powerful and very simple to use.
All of Shainin's techniques are strictly protected by copyright.
The only drawback to this strategy is that the per diem instruction rate can be expensive. A second drawback is Shainin's creation of "masters". A master is a senior certified problem solving specialist. This moniker has all of the same drawbacks as the Six Sigma "Black Belt" title.
Burns Bridge has had extensive Shainin training and has used their techniques many times to solve problems at many employers OEM automotive, three Tier 1 automotive companies, engineered pump manufacturing, aerospace and defense components manufacturing, plastics recycling, and rotating equipment repair service centres.
From the picture above, the phrase "let the parts do the talking", says it all. In the Shainin system what is wrong can often be seen by visually inspecting or dimensionally inspecting parts. When a part breaks or an assembly fails, it is very important to inspect the morphology and pathology of the broken part(s). The Shainin approach frowns on the use of fish bone diagrams to solve a problem. Fish bones define a million root causes and represent a "shot gun" approach where the solver tries to identify every possible root cause. With a fish bone, the process of finding the red X or dominant root cause becomes very laborious and time consuming, with the result that there is a high probability of failure. The Shainin approach is more that of a "rifle" where the solver systematically eliminates families of variation until there is one remaining.
The data collection and analysis work is extremely parsimonious. In the few circumstances where multi variate or design of experiments is needed, the Shainin methodology uses a very simple factorial experiment which involves a fraction of the experiments which would typically be conducted in a Taguchi study.
Statistical Engineering - University of Waterloo (BISRG): Formerly known as the IIQP (Institute for Improved Quality and Productivity), the BISRG provides training and consulting services to industry and business, advocating and teaching a problem solving methodology called statistical engineering. This system is also a binary problem solving strategy virtually identical to the Shainin Method. The advantage of this methodology over Shainin is one of training cost, as the BISRG instructors are a fraction of the cost of Shainin's instructors. Otherwise the methodologies are very similar. Accordingly, Burns Bridge recommends the Statistical Engineering problem solving methodology as the best of all strategies presented on this page.
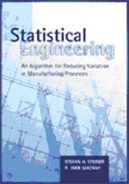
The New Science of Fixing Things: TNSFT is a relatively new consultancy. While their problem solving strategy was initially directed at the engineered to order manufacturing environment (batch quantity of one), they have since expanded their methodology to cover volume manufacturing cases. TNSFT espouses an energy consumption approach to a machine to analyze how energy is used or consumed in a machine to arrive at a root cause. More recently this has evolved to understanding how something is designed to work versus how it is actually working. A basic tenet to solving any problem in a process or machine is that you must first understand how it is supposed to operate. This idea is absent from the previously described problem solving strategies.
Burns Bridge has not received any formal training in this methodology. However their ideas and approaches expand or add to the problem solver's tool box.
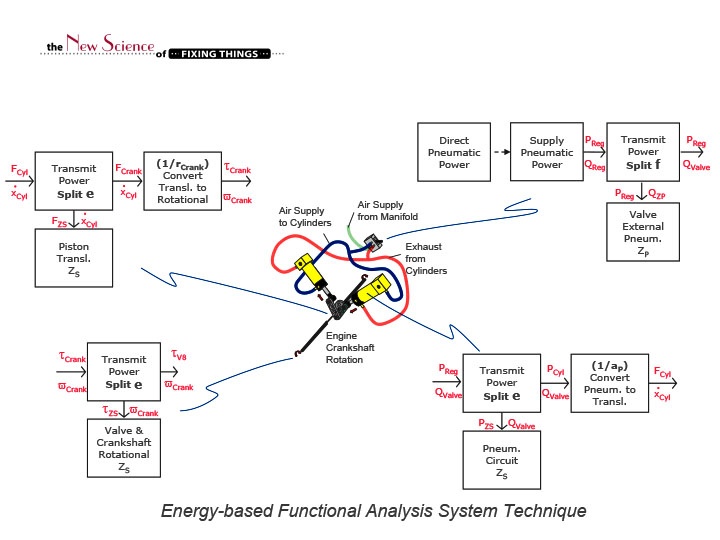
Closing Comments: As a problem solving practitioner for more than 35 years, Burns Bridge has worked in factories and solved problems in a few days or a few months which have existed, tragically, for as long as 35 years. The root cause of such long lived problems is believed to be a negative work place culture which is adversarial and which discourages good teamwork and communications.
In the five strategies outlined here, the most expensive and time consuming strategy, six sigma, will deliver results in one to two years, worst case. In a 38 year career, Burns Bridge has only encountered one esoteric problem which did not have a neat tidy solution (poor machining insert life caused by poor micro-structure in hyper-eutectic aluminum silicon alloy). Burns Bridges' experience is that the majority of problems can be resolved in a week with a few taking up to six months and only one taking two years to solve. Problems taking longer than a month to solve generally involve organizational and managerial road blocks which slow down the problem solving journey.
When working to solve a problem, it is always best to park one's prior personal experience (bias) and start with a "blank sheet of paper", that is, with no preconceived bias whatsoever.
Burns Bridge understands the critical need to use data to solve problems and make decisions. The assessment of what data to collect and how is one challenge. Interpreting the data collected is an even bigger challenge. It is easy to conclude that a problem has been fixed when all that one has observed is "noise". A big problem is how to tell if one has observed a signal (a significant change in the process) or noise (no change at all in the process). Every process contains a characteristic called the signal to noise ratio. The larger this number the stronger the signal that you have effected a change or made an improvement to the process. Accordingly, Burns Bridge strongly recommends that any problem solving practitioner read:
Understanding Vibration: The Key to Managing Chaos, by Donald J Wheeler. This book provides an excellent primer on the pitfalls and ins and outs of data interpretation.
Further, when training a group of employees, only 20% or fewer will take up the methodology after the training either in the office or the shop floor. These employees regardless of their education level, are your agents of change. They should be rewarded with more training and coaching as they will lead the charge to solve problems in your organization. This is again a Pareto effect where 20% of the employees will generate 80% of the ideas.
Burns Bridge does not advocate selecting only "agents of change" for training. As a minimum training should include all possible agents of change, and an additional representative group of employees. Training additional employees will head off much resistance to change down the road.