Kaizen Blitz
Kaizen Blitz: An introduction and some words of caution
A blitz can be a quick and productive way of achieving change and improvement in the workplace provided worker and employee support is present. If there is cost cutting which results in manpower reductions, employee participation in such exercises will be zero and in many cases, employees will act to sabotage the process.
While the blitz is intended to yield results in one to two weeks, problems requiring a longer time frame and a cross functional group of employees might be better approached as a problem solving project. Such projects are much less formal and can yield solutions to most problems in less than 30 days.
Key ingredients needed for a blitz to be successful are outlined in the graphic below.
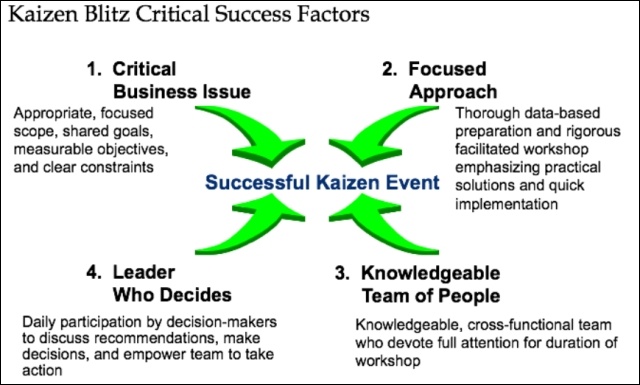
The graphic below details how to conduct a blitz.
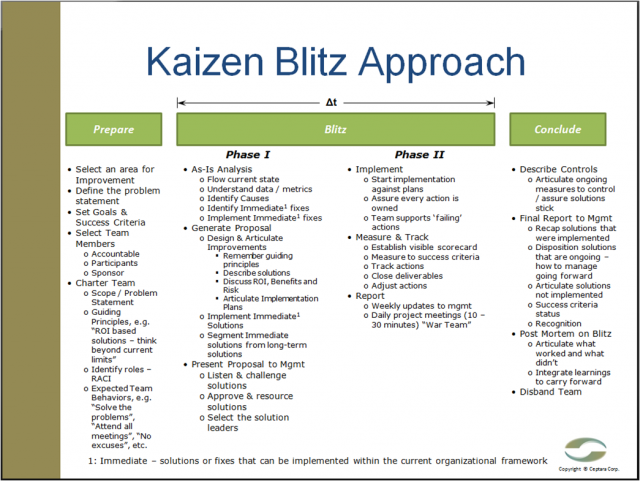
Kaizen Example - Liquid metal spillage in OEM automated piston casting process:
An automated gravity permanent mould piston casting process with 8 machines, two holding furnaces and four hydrualic actuated three axis pouring mechanisms needed to produce 12000 pistons per day on three shifts five days per week. A manufacturing engineer on his first day on the job, felt it prudent to meet with the employees on the casting deck to obtain their list of problems which should be fixed. In preparation the engineer had a clipboard with a squared note pad (a blank sheet of paper).
The meeting lasted less than sixty seconds. A spokesperson for the group said fix the "expletive deleted" ladles. When asked for elaboration, the engineer was advised to go and watch the automatic pouring ladles himself. Subsequently, the employees left the room.
After watching the ladles pour metal for an hour it was evident that due to backlash in the 90 degree actuators there was a lack of precise alignment with the ladle and the mould sprue openings with the result that liquid metal was being spilled on the moulds and the water hoses providing cooling. As evidence of the leaky water hose problem there were small stalactites on the roof deck 45 feet above each machine caused by water explosions from leaking hoses.
Moments later the electrician said he new what the solution was and had not been able to convince staff to implement it. He indicated that the use of a pin and bushing arrangement could maintain precise alignment at very little cost. After a quick meeting with the tool makers and the electrician, agreement was obtained on an appropriate design. A week later a prototype set was installed on one ladle and two casting machines with excellent results (complete elimination of metal spillage). Subsequently, the other pouring robots and casting machines were similarly outfitted.
With this "test problem" addressed, in the second meeting with the casting deck employees, a more complete and prioritized list of their operating problems was obtained. Over the next 24 months the casting deck was able to boost throughput from 6000 to 16000 pistons per day. Employee participation here was enthusiastic because the initial operation was so problematic the employees spent 100% of their shift working hard to keep the process running. In the end case, less than one hour per shift of work was needed to keep the process running. Operators could spend the other seven hours reading a newspaper.
Use of the Kaizen blitz to address the structural issues with this shop would have failed. The solution to the liquid metal spillage problem was beyond their control. The use of a problem solving group was far more effective.