Business Turnarounds
Burns Bridge has a decades long experience of turning around organizations and processes. In 1988, he was informed that he was an agent of change. In the intervening years Burns Bridge has effected substantial improvements in process, quality, delivery and the bottom line regardless of the employer or process. Examples of some of these improvements are given below.
1. Glass Container Plant (600 tons per day): In the 1980's at Domglas' Hamilton On plant in various positions from 1980 to 1982, Burns Bridge achieved a reduction in controllable process lost time from 18% to less than 2% (on a bad day). Through this period site labour went from 1100 employees to approximately 700 while percent pack improved from 50-55% to over 90%. With speed improvements due to bottleneck mitigation, an almost doubling of throughput from sales of 75 million to 150 million was achieved. Through this period the bottom line improved from minus 15 million loss to 36 million profit. This performance continued through to mid 1986.
With a furnace rebuild and the installation of new technology the performance of the plant slumped back to 1979 levels. Once again a turnaround restoring the plant to good performance metrics was again effected, this time in less than 9 months.
2. Brampton Foundries (jobbing aluminum foundry): As engineering manager, Burns Bridge's stepped into a money losing operation on a list of plants to be closed by its parent owner. Assuming in short order additional responsibilities for all tooling, maintenance, engineering and quality issues, a core team of junior technical staff was built, to transform the operation. Initially the foundry had a quoted lead time of six months, was chronically late on all shipments, had serious internal and external quality problems as high as 80% and was perceived as being expensive by the majority of its casting customers.
Over a five year period the following metric improvements were achieved. Work cell manufacturing was implemented reducing the needed floor print from four buildings and 80000 square feet to two buildings and 40000 square feet. Pounds shipped went to 2 million from 1 million per year. Primary processes were rationalized from 15 down to 7. Pouring yield increased from 25% to an average of 60%. Internal process scrap decreased to under 8% from over 60%. Total manning decreased from 167 to under 65 employees. Lead time was reduced to five days. The plant proceeded to operate at a break even level from being a chronic money loser. These improvements represented an almost 4 times productivity improvement.
3. GM Powertrain (St. Catharines Engine Plant - 5.7 liter piston casting cell): In 12 months Burns Bridge's achieved the following improvements. Reduced piston casting scrap from 16% to under 4% (engineering process scrap only). Achieved a doubling of throughput from 6000 pistons to more than 14500 pistons per day. Achieved a complete elimination of productive and maintenance overtime in a plant where all other cells worked 7/24 per week. Reduced furnace maintenance spend from $250000 per annum to under $25000. Tripled cutoff insert life from under 500 pieces to more than 1500 pieces. Achieved a reduction in durable tooling spend from over $250000 to under $20000 per annum. Achieved a two thirds savings in perishable tooling costs.
Later, on the rod and cam machining lines resolved a number of bottleneck and machining component quality issues which had beset these component machining lines from 25 to 35 years.
3. Niagara Machine Products (Tier 1 machining of transmission spool valves): As manager of the blanking screw machine shop having 72 employees, 36 multi spindle screw machines and several single spindle CNC machine tools achieved the following improvements: 1. A more than 50% improvement in throughput. 2. Setup a tool room to systematically store gears, cams and tool holders reducing setup time by 40%. 3. Achieved a 95% reduction in aluminum bar machine tool downtime by addressing supplier quality oil coating issues with the bar stock. This eliminated broken carbide inserts taking their life from 3500 pieces to multiple 40000 piece runs. 4. Achieved a 90% reduction in iron bar screw machine downtime by implementing lubricious coatings on drills and radial inserts (eliminated raw material pickup). This took drill and insert live to more than 10000 pieces from less than 1000 pieces.
4 SKD Automotive (Tier 1 Stamping and robotic weld assembly plant): Managing over 45 staff (tool and die makers, plant maintenance and robotics technicians) Burns Bridge stepped into an operation beset by the following problems. 1. An epidemic of smashed stamping tools and a tool room chronically over budget by 100% every month. 2. A press shop with an efficiency of less than 25% due to a glacial die change process taking more than 24 hours. 3. A weld shop having over 60% rework. 4. The site's on time delivery record was less than 97% and $70000 in premium freight was being incurred each month.
Within 7 months, the on time delivery improved to 100%. Due to a wide variety of weld shop common cause and special cause process improvements, weld rework dropped to well under 10%. At the same time the site achieved a 20% increase in sales (new product) without having to hire anyone. With the implementation of a die protection program in the press shop, the epidemic of smashed stamping tools was arrested. The tool room started to run under budget for the first time in its 15 year history. Together, with very modest improvements to the changeover process the press shop efficiency more than doubled to over 50%.
Most significantly the bottom line number for the plant improved from $12 million to almost $23 million per annum.
5. Fluid Motion Technology Div. of Martinrea (fuel and brake bundle fabrication plant): Managing 13 technical staff, the following results were achieved:
- A more than tripling of the bottleneck speed (leak testing) with an attendant almost two thirds labour savings.
- An elimination of first time through leak test failures.
- With the installation of light curtains to replace two hand palm button controls, eliminated pinch injuries in the shop.
- Achieved an almost doubling of pack density saving at least $1 million per year in internal material handling, over the road freight and end customer material handling.
- Achieved 0 parts per million defective through a period from mid 2004 to mid 2005.
- Achieved an elimination of maintenance and productive overtime.
- Achieved a 100% on time delivery for PPAPS, quotes, prototypes, ramp parts and production parts through three consecutive years.
- With these improvements the plant was able to maintain its position as the most profitable of 17 Martinrea plants at a time when the customer was demanding 20% off the price, the Canadian dollar exchange rate had moved against the operation, and oil was surging to over $100 per barrel (the plant made parts for full size vehicles for several GM platforms).
5. Flowserve Canada (Worthington Engineered Pump Plant - Brantford) : Managing four supervisors and up to 60 plant skilled trades and working with fellow manufacturing engineering and quality managers the following was accomplished:
- A cost of quality reduction from 6.5% to well under 1%.
- An improvement in on time delivery for pumps and parts from 35% and 50% to 95% and 98% respectively in less than two years.
- Record bottom line performance for four years in a row 2006 to 2009.
- An almost total elimination of mechanical seal failures in assembly, on the test stand, and at startup at the customer.
- Improvement in on time delivery of all aerospace components from 0% to 100% in less than 3 months.
- A quadrupling in high speed machining throughput of Dreamliner engine nacelle assembly latch beams from 1.5 per week to 6 per week, removing Cormer from Goodrich Aerospace's list of problematic suppliers.
- Budget plan bottom line was increased by another 37% beating budget by 45%.
- A quality system was created and installed, culminating in a receipt of
quality system certification from Flowserve for "B" level repairs.
- The Edmonton shop was moved into
new quarters.
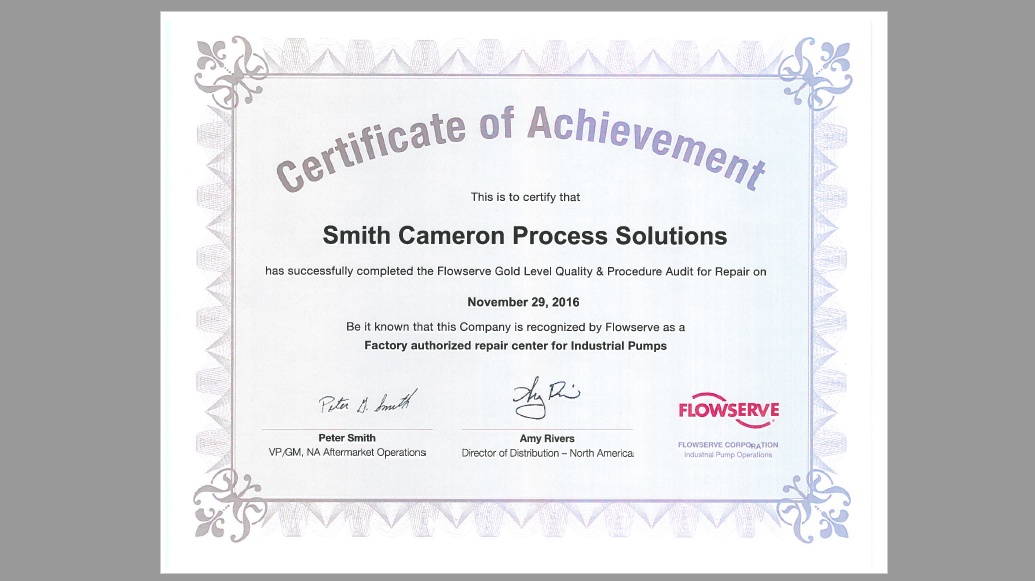
Summary: Over a 38 year career, Burns Bridge has learned that aggressive change can be accomplished, provided employees are treated with a high level of trust and respect. As long as their employment is not in jeopardy and their ideas are listened to, and where they have substance and benefit, implemented, employees will actively participate in and support the change process. Employees in today's internationally competitive free trade environment are acutely aware of their employers' needs to innovate and improve productivity. They understand that with improved productivity and quality, comes improved job security.