5S Housekeeping
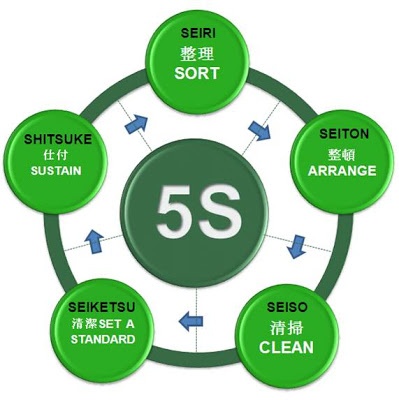
Burns Bridge has effected substantial improvements to housekeeping in every position and location he has worked. In every case there have been substantial improvements in safety, cost and productivity. Burns Bridge understands the in and outs of 5S safety and how such management driven programs can fail. Burns Bridge can help you with your housekeeping and productivity improvement initiatives.
Comments:
- The critical importance of housekeeping in an organization cannot be overstated.
- A clean well organized plant is an efficient and intrinsically safe operation.
- To this end, an organization's culture permeates from top to bottom. If it maintains a high level of housekeeping at all times, there is a high probability that their business processes are also highly organized and efficient.
- Employees will take better care of assets without being asked in a plant with a high level of housekeeping and cleanliness.
- When customers visit, their main observation in a plant is its level of housekeeping. Customers upon seeing a high level of housekeeping will treat their suppliers with a much higher level of trust and respect. If they see a messy factory or office, they will conclude that the vendor is less than competent and error prone. Thus a vendor can fool a customer if they have good housekeeping and poor quality processes. Thus good housekeeping can buy a vendor time to fix their internal processes.
- Some organizations have added a 6th "S", safety. In all organizations today, employees' health and safety is touted as the organization's number one priority.
- Finally, many first time readers of lean or TPS, latch onto housekeeping as the main element of improvement. Focusing solely on housekeeping produces a clean plant, but passes by all of the other very important components of lean manufacturing strategy. Good housekeeping is but one small part of lean.
- 1980's bottle plant mould repair shop.
- 1990's aluminum jobbing foundry restructuring.
- 2012 to 2014 OEM rotating equipment repair shop.
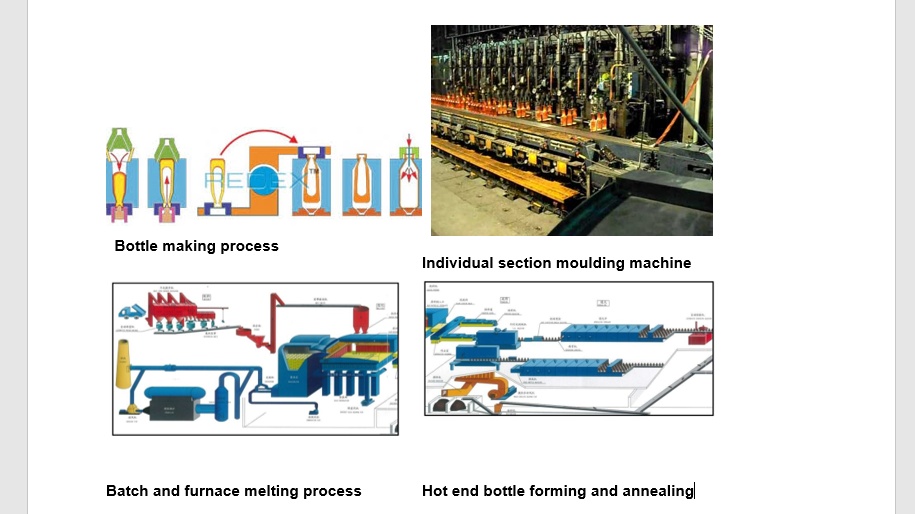
Glass Plant Mould Shop Housekeeping Improvement:
Before Situation: A mould repair shop in the mid 1980's responsible for the repair of 20-22 sets of glass container moulds per week was chronically late getting tooling up onto the production floor three days in advance of a job change on one of 12 glass moulding lines. The shop had the following housekeeping problems:
- Lack of adequate mould pallet storage space with over 60 pallets of tooling stored on the floor interfering with material handling (narrow aisle electric fork truck and presenting a safety trip hazard to pedestrians.
- The shop had received permission to scrap over 200 pallets of obsolete tooling but had thrown nothing out over the decades.
- The shop walls were dirty and water stained from a lack of a fresh coat of paint in perhaps 30 years.
- A paper laden filing system which required two people to carry relevant files to thrice weekly meetings.
- A storage room in the rear of the shop which contained obsolete electric motors and racking was cleared of everything (all material was sold as scrap).
- New pallet racking was installed similar to existing mould storage pallet racking.
- In parallel, a senior employee was assigned to sort through the 200 pallets of obsolete tooling and retain any components which could be redeployed as spares on other jobs.
Aluminum Sand and Permanent Mould Foundry Cleanup 1990:
Before Condition: A jobbing foundry in the 1990's was producing poor quality castings, late and more expensive than their competitors at a time when customers were able to shop around and obtain quotes having a 30% discount. The foundry was in danger of closing due to poor economics.
The site consisted of a total of four buildings of size 20000 square feet each with a die cast plant in the one building 2 miles separate, and sand and permanent moulding process in the other three buildings located on a second site. This case only concerns the cleanup of the sand and permanent mould operations.
The sand and permanent mould site was cluttered from one end to the other with all matter of detritus not germane to an efficient foundry. The level of junk and waste was such that lift truck material handling was inefficient.
Action Items: In early 1990 a small economic recession together with competitive pressures forced the need to lay off 35 employees. Rather than give employees pay in lieu of notice, a decision was made to have them work through their respective notice periods of 2 to 9 weeks.
- The employees were organized into groups of seven to some extent by nationality with at least one individual speaking English.
- Three lift trucks were rented.
- Three sets of gas oxy-acetylene torches were rented.
- A list of obsolete tooling was prepared (most tooling was customer owned). Unless the customer was bankrupt, tooling could not be scrapped without written customer authorization.
- Three cans of spray paint, red (scrap), yellow (hold for review) and green (keep) were used in multiple passes through the 9 week period to identify material.
- Five different scrap bins were procured for such items as garbage, wood, iron, etc.
- Employees were trained how to drive the trucks and use the cutting torches.
- On time delivery improved to 100% on time from 100% late.
- Customer returns were reduced to a fraction of a per cent from up to 80%.
- Internal casting scrap was reduced to less than 8% from as high as 80%.
- Lead time was reduced to 5 days from six months.
- Manning was reduced from 167 to less than 65 employees while pounds shipped increased to 2 million from 1 million per annum.
- The building footprint was reduced by 50% to 40000 square feet.
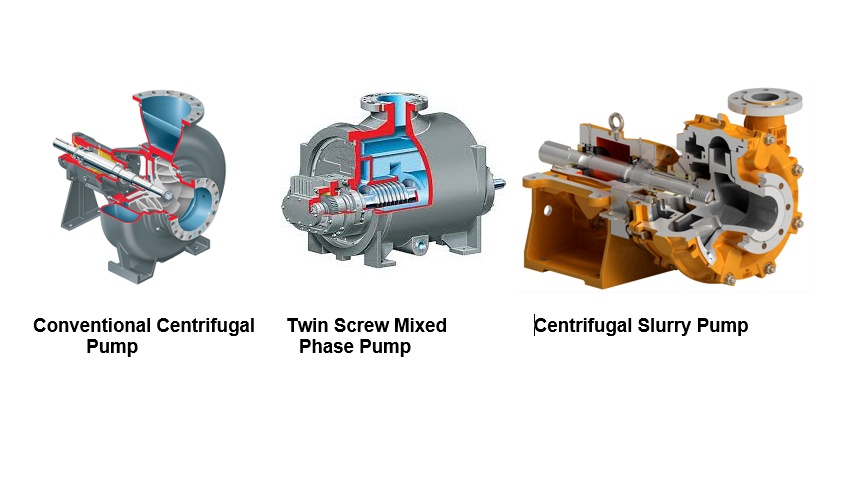
OEM Rotating Equipment Repair Shop: Above are typical examples of engineered to order rotating equipment. Below is a layout of a typical repair shop. Basic processes are receive, inspect, quote, weld, machine, reinspect, assemble, package and ship. The housekeeping of the shop could be best described as "organized clutter".
Before Condition:
- The shop over a period of decades had accumulated a large amount of scrap material (shafts, castings, bearings seals) which were obsolete due to replacement with new. Many job boxes were filled with scrap material with no job boxes available for new work.
- The shop had inadequate rack storage with over 40 pallets of customer owned material stored on the floor all over the shop.
- The outdoor yard contained many pallets of obsolete or scrap material.
- There was no process for scrapping obsolete customer owned material on each job.
- A paint campaign of red, yellow and green was again organized to identify material which was obviously scrap (red), material which may require customer permission (yellow) or material which should be retained (green).
- All job boxes were brought to floor level and emptied of any scrap material.
- The yard was laundered with paint colours as necessary.
- A clause was added to every quote which allowed the site to dispose of surplus and scrap customer owned material if no guidance had been received from the customer by day of shipment.
- Additional new rack storage was procured and installed in the shipping department adding over 75 storage slots to the rack inventory.
- Several tours of the shop were conducted identifying more items for the scrap bin. This is akin to peeling away layer after layer of obsolete items. As many items are removed from the shop, more items appear as candidates.
Final Condition:
- 90% of the clutter was eliminated.
- All material could now be stored on racks with ample spare storage slots.
- There was now an ample supply of empty job boxes to handle new work.
- With the bulk of material now stored on racking instead of the floor, the shop was intrinsically safer for pedestrians.
- An increase in capacity to do additional work was achieved.
- Revenue from scrap sales paid for a golf tournament, a December holiday party and all weather parkas for everyone with ample funds to spare.
- With the new clause in each quote, scrap material from repairs was disposed of the day following shipment.
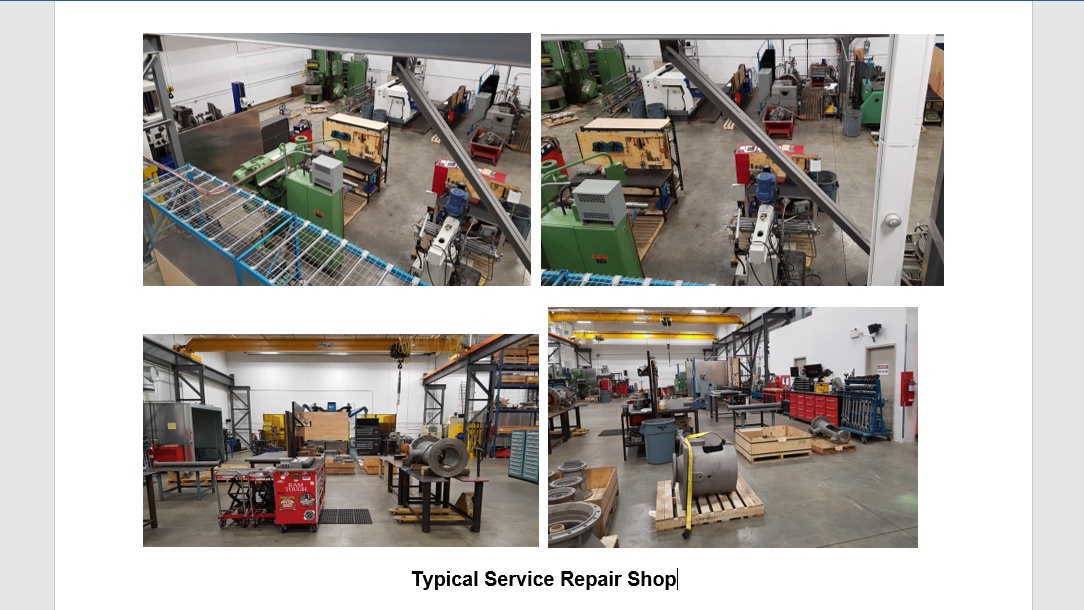